

Both have black fibre-faced bobbins and large flush pole-pieces. The humbuckers - Anderson's H1-A and H2+A at neck and bridge - mount directly to the body with dual screws on the bass side so they can be placed exactly parallel to the string angle. I also added pre-machined grooves of an appropriate size for each string." I also wanted a longer string ramp so we had the saddles made about twice as long. The bridge is aluminium and sounds much more lively than the zinc bridges others offer.
TOM ANDERSON GUITARS MODS
He agreed to make some mods that he also incorporated into his 'standard' bridge. "Steve is a mad scientist type, and he's also studied old guitars and can play. "I had tried the Tone Pros wrapover but there were some things I would have changed," says Tom. Here, however, it's made by Steve Rowan of Pigtail - a one-man shop in Colorado. The bridge isn't a million miles from modern adjustable wrap-overs from PRS or Tone Pros.
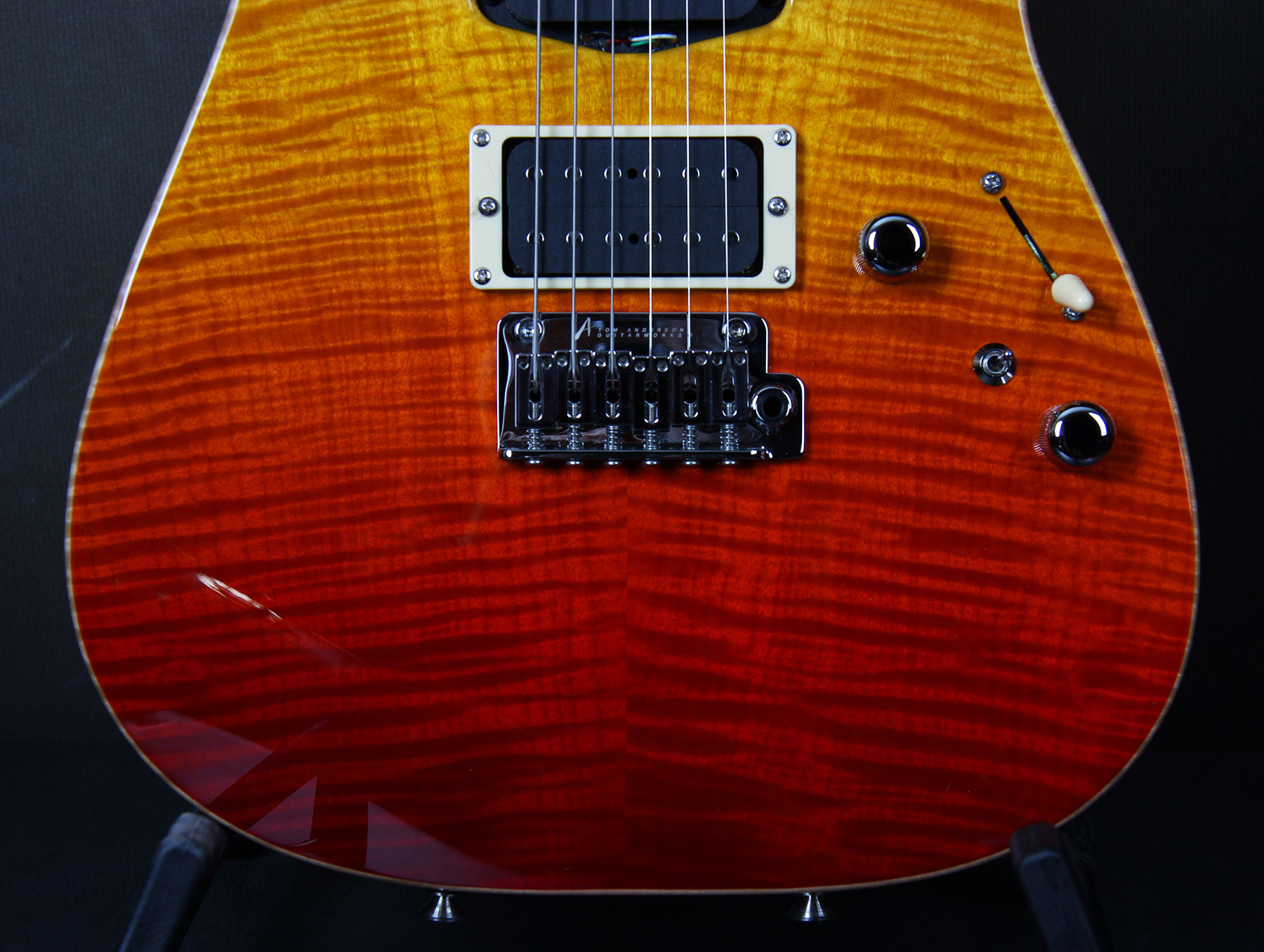
There's actually more surface contact with this joint than the traditional Fender style, and with our production methods, the precision angles are easy to keep correct." The bolts are a size larger than the traditional wood screws used on our other guitars, and these are machine screws mating to steel threaded inserts inside the neck.

"I'd have used only one screw to hold it on, but the adjustable rod is in the middle of the neck so I used two bolts offset of the rod by about 6mm. It cannot move sideways or longitudinally." Our joint is a compound wedge, so it requires no pressure at all to keep the neck in proper alignment. The Fender-style joint, even when executed well, doesn't really hold the neck in position very well. "I've been thinking about a new neck attaching method for many years.
